表面粗さについて~ Ra? Rz? RzJIS? 『表面粗さ』をわかりやすく解説します☆
表面粗さとは、加工面の状態(凸凹具合)を表す指標で、機械加工した製品の表面の滑らかさ・粗さを評価するときに使われます。その機械加工にも様々な加工が存在します。
今回は、その表面粗さと、仕上げ記号について、お伝えします。
アンビル Ra0.04 Rz0.4
なぜ 『表面粗さ』 が必要なのか?
製品の表面粗さを自分以外の他人に伝える際に、『表面がツルツル・ザラザラしている』などといった表現でも、何となくの雰囲気は伝わりますが、実際の正確な表面の状態はわかりません。
見た目や手触りでは、どうしても人による違いや誤差が生じてしまいます。
面精度が要求される場合、誰にでも同じように伝わる必要があるため、
数値で規格化されたもの使う必要があり、それが表面粗さです。
この表面粗さは面粗度と呼ばれることもあり、JIS B0601やISO25178にて規格化されています。
表面性状パラメータ
以前は、表面粗さを表す記号として、逆三角形(▽・▽▽・▽▽▽・▽▽▽▽)などで定義されていましたが、現在では数値化されたもので規格化されています。
(実際に現場で使用する図面の中には古い図面もあるため、旧規格と現在の規格が混在している状態ですので注意が必要です。)
現在の表面粗さは『Ra』・『Rz』などといった指標で
『Ra 0.8μm』などのように表され、この数値が大きいほど
ザラザラしている・または凹凸が大きい状態で、光の反射も鈍い状態であることを意味します。
逆に、数値が小さいほど表面が滑らかで、凹凸が小さいことを表しています。鏡のように加工(鏡面加工)すると、数値は 小さくなっていきます。
表面粗さ標準片
表面粗さを表す指標として、平均値を用いた
『算術平均粗さ(Ra)』や、大きい山と深い谷の差から算出する『最大高さ粗さ(Rz)』など、用途に応じた粗さパラメータが多数存在します。
代表的な表面粗さの種類
●算術平均粗さ(Ra)
Raは、粗さを表す指標としては最も多く使用されるパラメータです。
中心線から上の凸部分の面積と、凹部分の面積を足し、基準長さで割って凹凸の面積を平均化したものを差します。
Rough average(粗さの平均)と覚えると分かりやすいです。
平均値なので、突発的に発生した大きいキズの影響は受けづらいと言えます。
●最大高さ粗さ(Rz)
中心線から一番高い凸部(Rp)と、一番低い凹部(Rv)の合計値になります。
同じ部分を測定したとき、Raよりも数値が大きくなります。
Rzは、突発的に発生したキズの影響を大きく受けるので、一カ所でも大きな傷があると問題となる製品に
採用されるパラメータになります。
ちなみに、この最大高さ粗さは、旧規格の場合、RyやRmaxといったパラメータで表記されており、
今でも古い図面では見かけることがあるので、加工の際には違いを認識しておく必要があります。
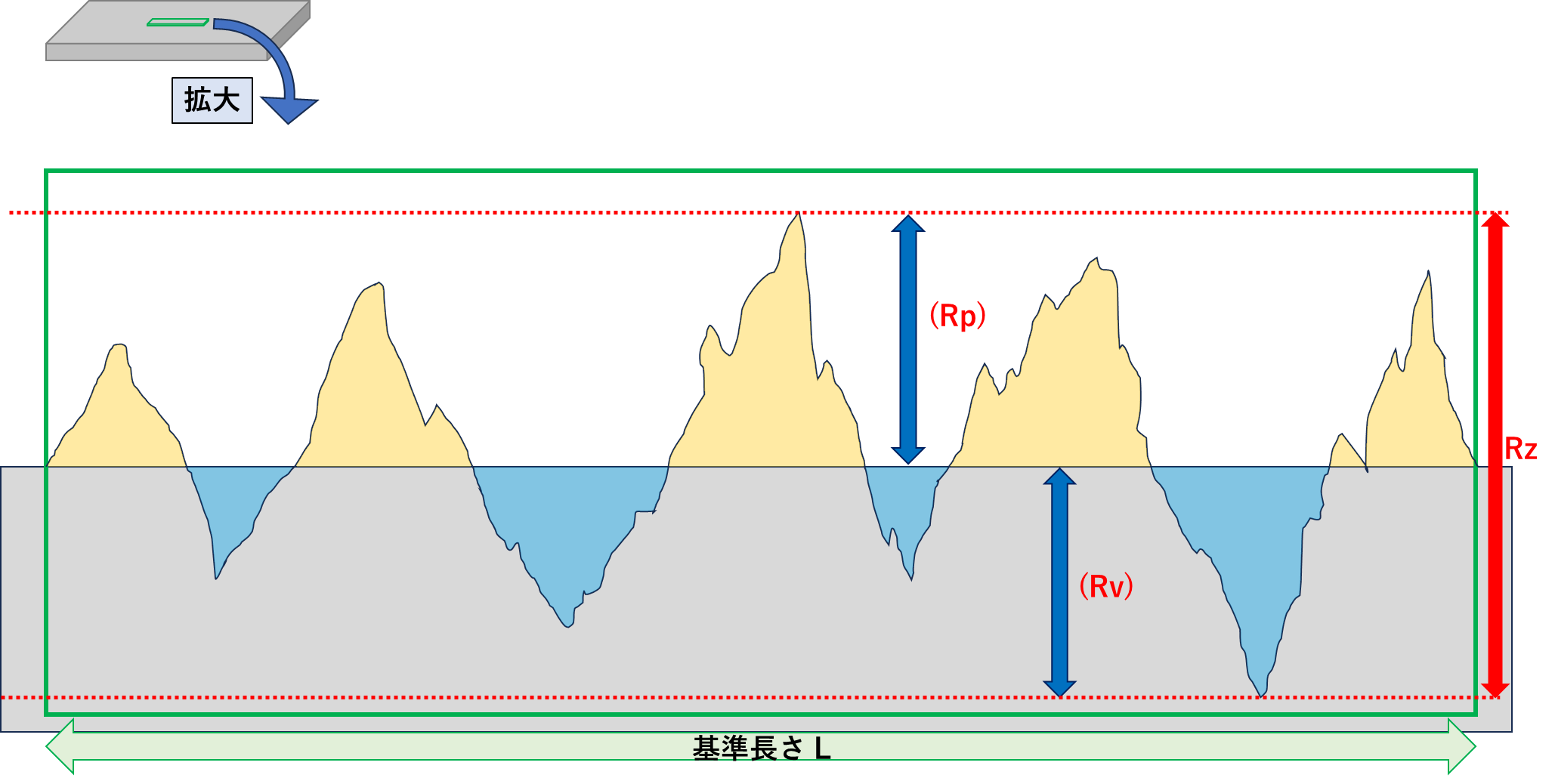
●10点平均粗さ(RzJIS)
中心線から一番高い凸部から5番目までの平均と、一番低い凹部から5番目までの平均の合計値になります。
旧規格(JIS ‘94)ではRzと定義されていたので注意が必要です。
現在ではISO(国際規格)からは除外されましたが、国内では広く普及していたこともあり、
JIS規格(日本国内)でのみ定義づけされています。
表面粗さの検査機器
以前は表面粗さの測定は、ページ上部写真のような「表面アラサ標準片」とワークを目視で比較して、面粗さを確認していました。しかしながら、現在では、粗さも、図面にて数値で指定されることが多くなり、粗さ計による計測が不可欠となっています。
粗さ計は、大別して接触方式と非接触方式があリます。
●接触方式
従来から主流であり、実績も豊富な粗さ測定方法です。スタイラス(触針)で表面をなぞって断面形状を取得します。粗さだけでなく、輪郭をなぞっての形状測定も可能です。ただし、接触の測定力が掛かります。
特殊超硬バイト 開発ラボでは、「表面粗さ輪郭形状総合測定器」 サーフコム NEX100 DX-12を用いて、
工具の表面や刃先の面精度を精密に測定して、研磨の品質を担保しています。
表面粗さ形状測定器 スタイラスにて超硬センターの表面粗さを測定
●非接触方式
レーザーや光、深度等を用いて行うのが非接触式の測定です。
こちらは、ワークにスタイラスが接触することなく測れるため、ピンポイントの測定や接触測定でチッピングのリスクがある刃先が鋭利な刃物に適しています。また、3次元の立体的な評価も可能です。ただし、内径や陰になる部分は測定できません。
特殊超硬バイト 開発ラボでは、「デジタルマイクロスコープ」 VHX-6000を用いて、非接触にて刃先の粗さや非常に緻密な形状の3次元測定を行っています。
デジタルマイクロスコープでのバイト刃先粗さ測定 粗さ測定結果画面
特殊超硬バイト 開発ラボにおける『工具表面粗さ・刃先粗さ』の重要性
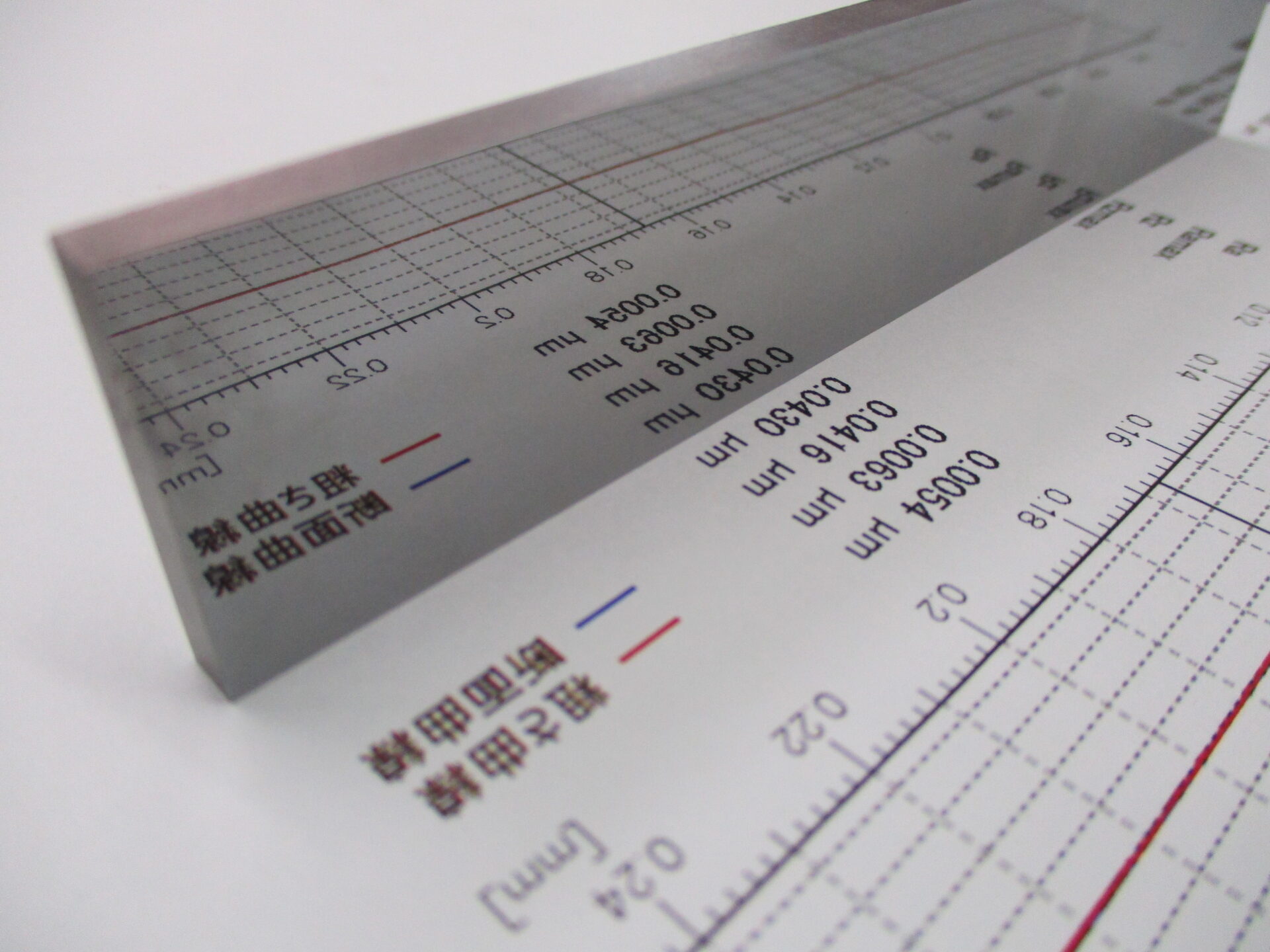
表面粗さが異なることで、どのようなことが起こるので
しょうか。
例えば、表面粗さがRa0.05になってきますと、外観的に
見た目がキレイで光の反射が鋭くなってきます。
Ra0.01~Ra0.02まで来ると、鏡面加工といった鏡のような仕上がりになってきますが、このあたりの数値になってきますと加工が難しく、一般的に研削盤だけで仕上げることが困難となります。
特殊超硬バイト 開発ラボでは、
砥石メーカーと共同で専用砥石を考案・製作し、Ra0.01以下・厚み公差±0.5μmを実現させました。
(写真:Ra0.0054μm / Rz0.0416μm)
表面粗さが細かいことで、様々なメリットがあります。
●刃物の切れ味が格段に上がる
特殊超硬バイト 開発ラボでは、機械刃物のプロとして刃先加工実績が多数あります。
刃先の表面粗さを細かくすることで、刃物の切れ味を格段にアップさせることができます。
包丁を研ぐ時と同じ要領ですが、荒砥石・中砥石・仕上げ砥石といったように、砥石の種類を使い分けることで刃物の切れ味に変化が起こります。
家庭では荒砥石・中砥石程度(~#1000)で済ませて、満足とされる方も多いとは思いますが、
それ以上の切れ味を求めるには、更に粒度が細かい砥石にて仕上げる必要があります。
特殊超硬バイト 開発ラボでは、お客様のご要望に合わせた加工を可能にするため、様々な砥石をラインナップしており、機械刃物のプロとして刃物の切れ味にこだわっています。
●刃こぼれしにくい
表面粗さが細かくなることで、刃こぼれ(チッピング)が抑制できます。
刃こぼれしないということは、先に記述したように、『切れ味が良い』というだけでなく、『寿命が長い』という
メリットにもなります。
●高精度な寸法公差が可能
一見、粗い砥石でも高精度な寸法公差での加工はできるのですが、実際の表面に凹凸があることで、
摩耗しやすい・熱膨張の影響を受けやすい・測定器が馴染みにくいなどの理由から、測定値が安定しないことが多々あります。
結果として、公差の厳しい加工品であれば必然的にある程度の表面粗さに仕上げる必要があります。
●スムーズな動作で長寿命・コストダウン
部品同士がこすれ合う製品であるとするならば、凹凸が少ないものの方が表面の摩擦が少なくなり、
部品同士がスムーズに動きます。
また、こすれ合わないとしても、ワーク表面を使うことで擦り減る摩耗量が多くなり、工具寿命が短くなります。
これは、表面に凹凸があることで見た目には『面当たり』しているように見えて、実際には圧力が『点当たり』していることにより、集中的に『点』に大きな力が加わり摩耗を早めます。
表面が滑らかであるということは、それだけ負荷がかからずに使用することができるので、強度が強いことに加え、コストダウンにもつながります。
●錆びにくい
凹凸が少ないということは、表面積が小さくなる・さらに凹部分にサビを引き起こす成分が残りにくいという点から、サビづらい表面性状だといえます。
表面粗さ(面粗度)に関する製品事例
続いて、実際に当社が製作した表面粗さ(面粗度)に関する製品事例をご紹介いたします。
ⅰ.受けガイド | <加工ポイント> 1) Ra0.005 Rz0.04 の砥石による・・・・・ |
ⅱ.超硬スリットカッター
| <加工ポイント> 1) #3000ダイヤモンド砥石により、Ra0.006の・
|
ⅲ.角度溝入れバイト | <加工ポイント> 1) #2000の砥石・・・・・
|
表面粗さに関連する技術コラム
特殊工具の開発・製造のことなら、特殊超硬バイト 開発ラボまで!
今回は、表面粗さ・仕上げ記号についてご紹介しました。
表面粗さについて正しくおさえていただき、加工条件にあった適切な工具選定の参考にしていただけたらと思います。
特殊超硬バイト 開発ラボでは、高品質工具、複雑形状、長寿命な「きれもの」づくり、そして「まごころ」をこめて1つ1つ丁寧に特殊バイトを製造・開発してきました。創業60年の歴史と経験から得られる実績と高い技術力を有しています。
ロウ付バイト・総型バイト、成型バイト・溝入れ丸バイト、スロッターバイト、ヘール加工バイト、スローアウェイチップ、成型チップ・総型チップ、特殊スローアウェイチップ、ハイススローアウェイチップ、カッター刃・切断刃、粉砕刃・固定刃・回転刃、パンチ・ダイス・スリッター、ロール・センタレスブレード、コイリングピン・ワイヤー線ガイド、接点・電極・耐磨耗部品 など幅広く対応、記載がないご依頼も柔軟に対応いたします。
「どこに工具製作を頼んだらいいかわからない」
「時間・工数が合わない」
「コストがあわない」
「対応可能な会社が見つからず困っている」
上記のようなお悩みをお持ちの方は是非当社に一度ご相談ください。